With lives literally hanging on the line, helicopter operators working in search-and-rescue (SAR), law enforcement and powerline maintenance missions know the importance of having reliable, safe equipment.
That’s why manufacturers of hoists, hooks and winches are looking to develop safer, smarter and more reliable hoist solutions that will help operators carry out every mission successfully.
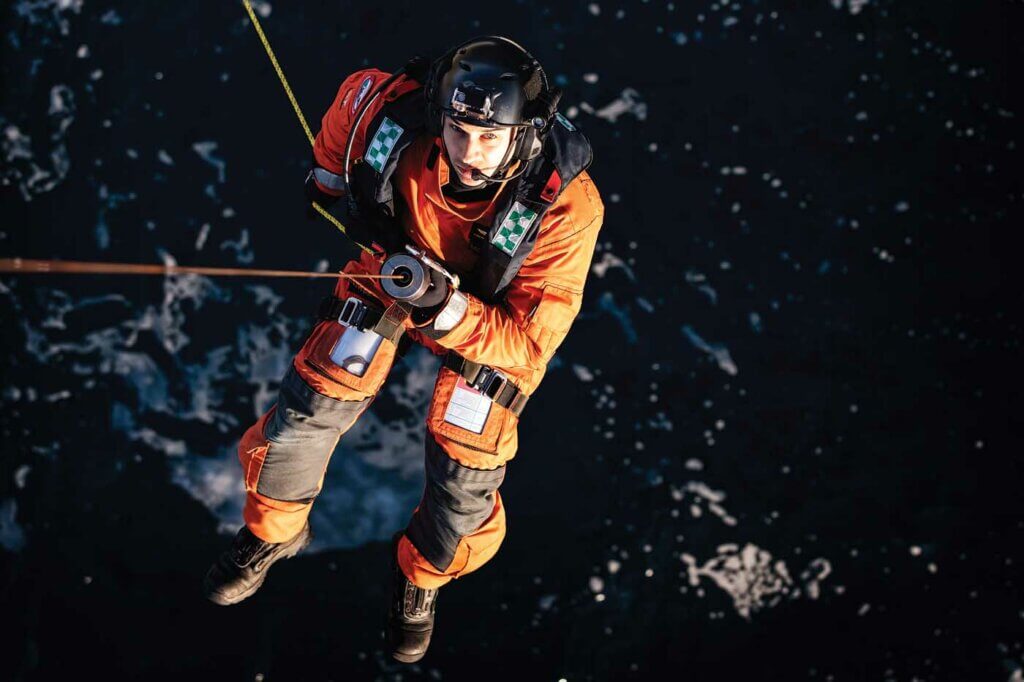
Collins Aerospace, an RTX business, is an expert in supplying equipment for human external cargo (HEC) missions. Its Goodrich rescue hoists are a common sight not only in the SAR and law enforcement sectors but also in transporting personnel to offshore wind turbines or powerline maintenance.
Equipped with more than 40 years of lessons learned and feedback from operators and maintenance technicians, Collins is developing the Pegasus — a next-generation rescue hoist system, designed to meet the new standards for helicopter hoist systems.
“A lot of time and effort was put in by a lot of different people to create the new standards, with a common goal of creating standards that will last for many years and will produce a safe, reliable hoist,” said Richard Bryson, technical capture manager for Goodrich hoist and winch at Collins Aerospace.
This effort stems back to 2014 when an SAE committee made up of hoist manufacturers, original equipment manufacturers (OEMs) and regulators, including the Federal Aviation Administration (FAA), European Union Aviation Safety Agency (EASA) and Transport Canada, came together to formalize standards for hoist equipment.
Six years later, SAE standard AS6342 was released in December 2020, expected to be adopted by the FAA for the Technical Standards Order (TSO). Once this happens, it’s expected to clear up any grey areas of the regulations and standardize the process for getting a hoist system certified and installed on an aircraft with the FAA.
EASA, on the other hand, decided to go down its own path. The aviation authority withdrew from the SAE committee in late 2019.
“There were a few things in there that EASA wasn’t happy with. They didn’t think it was detailed enough,” Bryson said.
In fact, its Notice of Proposed Amendment included 280 comments, initially with rules that seemed to be very different from the AS6342 in some key areas. But EASA released its own European Technical Standards Order (ETSO) in September 2022, which ended up being significantly closer to AS6342 than its original proposal.
Bryson said both the FAA’s and EASA’s standards formalized many of the rules the industry was already aware of but weren’t clearly spelled out in the regulations.
For instance, testing to determine cable strength was “poorly defined in the old standard,” Bryson said. As a result, the SAE committee agreed on a testing standard that resulted in a requirement for stronger cables, meaning the cables for new hoists will get bigger.
Along with stronger cables and a more defined cable strength and abrasion testing, both standards will require more data collection and sensors to measure load on the hook, slip clutch, and fleet angle exceedance.
“Our hoists are good for more than a 30-degree angle. Beyond that, the helicopter may start to have an issue,” Bryson said. “One of the requirements is the system needs to notify the operator as they’re getting close to 30 degrees so they can make better decisions.”
EASA’s ETSO differs from the standard that the FAA plans to adopt in a few key areas, including a requirement for an even stronger cable, a secondary load path, tighter fleet angle requirements, and more clutch testing.
As is the case in the aviation industry, the new standards only apply to new airframes and new hoist equipment in development. All existing supplemental type certificates (STCs) will remain untouched by the standard changes.
As such, “it will take a while for everybody to adopt these regulations [and for] operators to start to see the new hoists,” Bryson said, adding the standards will likely impact OEMs and hoist manufacturers more than operators and maintenance technicians.
“At the operator level, there will be adjustments but I don’t think it will be massive. It’s still a hoist. It does everything that it did before,” Bryson said. “If you are the first person with a new helicopter and a new hoist, there could be some certification delays because there are a lot of details to go through with certifying helicopters and hoists.”
With clearer regulations in place, Collins can now forge ahead with developing its Pegasus hoist system, slated to come to market in 2025 — about a decade after the initial concept was born.
The standards development gave Collins an opportunity and blank slate to design a next-generation hoist using its decades of expertise and knowledge, as well as feedback from operators and maintenance technicians.
“There’s a tremendous amount of engineering, testing and validation that has to go into a new hoist,” Bryson said. “I don’t think a lot of people understand just how much work and testing is done on something like this, because people’s lives depend on it. We are held to the highest reliability in the aerospace industry.”
Bryson was the program chief engineer on Pegasus for the first six years of the program. The team began working on the next-generation hoist in 2015, before the standards were even ironed out, so admittedly, they were working in murky water.
“Some of our early work has been thrown out, but some of that early work still carried all the way through,” he said.
Not only were they designing a system that would meet future regulations but they were designing a system for future operators. This even included redesigning the handheld control pendant to fit the hands of today’s diverse and inclusive workforce, realizing that the future of the sector may not be male dominated anymore.
“Our original hoist was designed back in the mid-1970s,” he said. “When we first designed the old hoists, nobody controlled a searchlight from their pendants, but now, we are integrating with that. We’ve taken a step back to look at how OEMs can better integrate the system into the aircraft.”
Bryson said the team has made thousands of revisions and upgrades to its hoist system, but there are still certain core aspects that reflect the basic architecture of a Goodrich hoist.
The Pegasus will feature durable components, modular architecture and new features, including a data acquisition sensing and health (DASH) system that monitors and records hoist parameters like load, speed, and temperatures. DASH could be integrated with the aircraft’s health and usage monitoring system (HUMS), or used independently through a smartphone or tablet.
“[Operators will] have more information than they have now so they can make smarter decisions,” Bryson said. “On the maintenance side, it’s designed to be easier and simpler for them to use as well.”
Available in DC and AC configuration to fit helicopters rated for a 600-pound (274-kilogram) capacity rescue hoist, the Pegasus will also feature a new drum and traction system that holds a 295-foot (90-meter) cable. The system is designed for improved cable wrapping under all load conditions, reducing wear and tear and extending the cable’s life.
“Every operator that I have ever met, when we talk to them about Pegasus, they are excited for it, happy to know some of the changes we’ve made,” Bryson said. “It’s a transition like anything, but it’s not changing the way you fly or the way you rescue. The basics remain the same.”